El nuevo robot para envolver lentes hecho gracias a componentes impresos en 3D
Santi sr es la empresa líder en la producción y distribución de bolsas de papel especiales para el sector oftalmológico.
Las bolsas Santi Envelope son utilizadas por laboratorios oftálmicos en líneas de envasado automático dedicadas al envasado de lentes. “Trabajando e interactuando con estos laboratorios durante años hemos notado falencias en el proceso de embolsado y la posibilidad de mejora en el flujo de empaque y envío. Entonces, casi por diversión y como reto, creamos Santi Solutions”, explica Manuel Mariga (COO de Santi).
Inicialmente la empresa colaboró con un taller mecánico externo para diseñar y fabricar los primeros robots para envasado automático. En una segunda fase, comenzó a construir las máquinas posteriores “en casa”.
EasyPack22 es la innovadora solución de envolvente y gestión automatizada de lentes propuesta por Santi Solution.
Esta solución está diseñada para procesar lentes tanto graduadas como de serie, convirtiéndose con el tiempo en un punto de referencia en la empresa gracias a su versatilidad y facilidad de uso.
Gracias a su tamaño compacto, EASYPACK22 es extremadamente versátil y eficaz gracias a la posibilidad de conexión al sistema de gestión presente en el laboratorio.
IMPRESIÓN 3D PARA PRODUCIR COMPONENTES PERSONALIZADOS
“Con este proyecto nos hemos acercado al mundo de la impresión 3D. Un mundo, hasta ahora desconocido para nosotros, con tanto potencial por descubrir, tanto desde el punto de vista del prototipado como de la producción”. Manuel Mariga explica
Inicialmente esta máquina era solo un prototipo, pero ya está en el mercado. Concebida y concebida por Santi srl, cuenta con más de 20 componentes personalizados según las necesidades de uso y todos estos componentes están realizados con la impresora 3D MarkTwo de Markforged. Las piezas impresas, listas en poco tiempo, se colocan directamente en la solución Santi para embolsado automático.
“Tan pronto como llegó la Mark Two, la imprimimos durante 60 días, las 24 horas del día, sin interrupciones. Necesitábamos las piezas para una entrega urgente y sin la ayuda de la impresión 3D la entrega se habría pospuesto.
Fue una inversión muy útil, tanto en términos de versatilidad como de reducción de costos”, continúa Mariga. “Los consultores de 3DZ nos acompañaron en la elección de la tecnología adecuada, brindándonos un asesoramiento óptimo para lograr el objetivo y asistencia técnica en todas las etapas de este camino”.
“Ha habido muchos beneficios de diseño y construcción con la impresión 3D”, enfatiza el gerente del proyecto Manuel Mariga
Los costes de las piezas individuales, a utilizar en la máquina, son considerablemente inferiores a los de una pieza fresada. Puedes ir desde 300 euros, hasta unos pocos euros (15-20)
Tiempos significativamente reducidos con la impresión 3D, en comparación con el método tradicional que requiere numerosos pasos. Ha pasado de semanas de espera a horas
Sin costes de almacén por repuestos. Cuando se solicita la sustitución de piezas, un día es suficiente para imprimirlas
Flexibilidad total en geometrías. Sin restricciones Se fabricaron piezas muy complejas, incluso con cavidades.
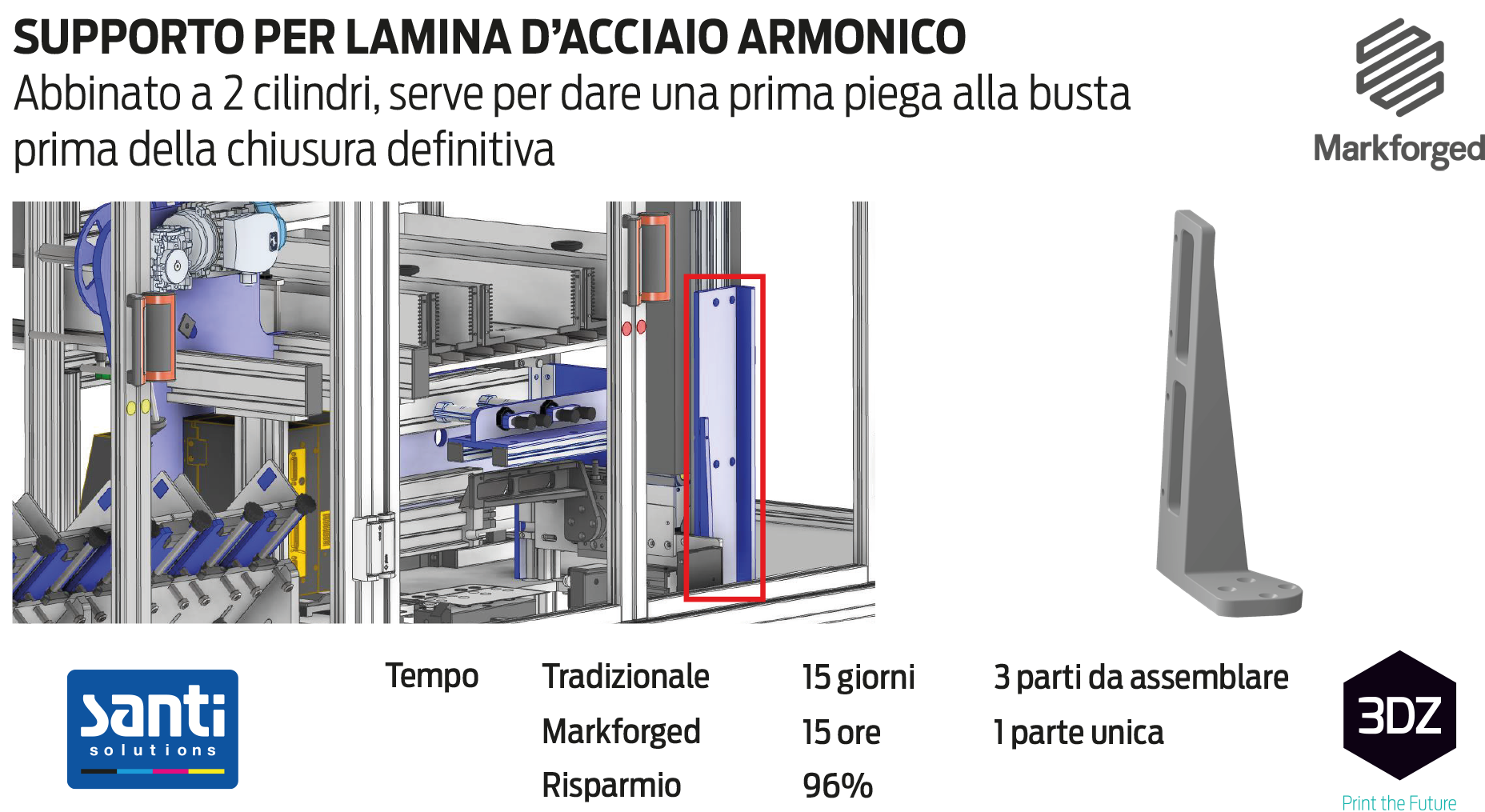
En el lateral, una foto de algunos componentes personalizados impresos en 3D
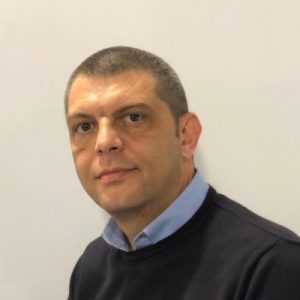
Santi Solution es una empresa de vanguardia, que ha descubierto las múltiples posibilidades de aplicación, la ventajosa relación tiempo/coste, así como el rápido retorno de la inversión inicial utilizando la impresión 3D, explica Gianfranco Caufin Area Manager 3DZ que siguió a Santi Solution en el proceso de ventas.
LA EMPRESA
Tras más de 20 años de experiencia en papeleras, en 1985 Valter Mariga da vida a la empresa de conversión de papel Santi srl. Al modificar algunas máquinas nacidas para hacer bolsas de papel normales, logra crear bolsas innovadoras para lentes oftálmicas. Inmediatamente encontraron una respuesta bienvenida en los laboratorios oftálmicos y fabricantes de lentes más grandes.
Los sobres para lentes se producen con máquinas especialmente modificadas, que fueron creadas originalmente para la producción de sobres comerciales normales. A lo largo de los años ha continuado un trabajo maníaco para mejorar la maquinaria desde varios puntos de vista hasta llegar hoy a 5 líneas de producción de muy alto rendimiento.