Alta productividad de piezas finales compuestas y repuestos con una impresora 3D de escritorio de rendimiento industrial.
Ordisi SA es una empresa catalana con más de 60 años de experiencia en la fabricación de equipos de electro-medicina. Están especializados en aspiración, con una amplia gama aspiradores, lámparas de exploración con luz halógena y led y lámparas para pequeña y mediana cirugía. Producen series cortas y buscan una forma de trabajar flexible que les permita adaptarse a las necesidades concretas y específicas de sus clientes. En la actualidad, exportan sus productos a diversos países de la U.E. así como en otros continentes.
El reto
La sfida per Ordisi è arrivata il giorno in cui un collare nello snodo di un apparecchio di illuminazione ha cominciato a danneggiarsi. Era necessario trovare un modo rapido ed efficiente per sostituire quel pezzo, evitando che la logistica dovesse far rientrare le attrezzature da tutto il mondo per effettuare la riparazione. Inoltre, il problema aggiuntivo era che per sostituire il pezzo, l’apparecchio doveva essere smontato, cosa che poteva essere fatta solo presso lo stabilimento di Ordisi.
La solución
La logística de traer de vuelta los equipos a las instalaciones de Ordisi, suponía un gasto importante, considerando además que estos se encontraban en diferentes países. En lugar de volver a fabricar la junta y proceder con las reparaciones, volcaron sus esfuerzos en diseñar una nueva versión que solucionara, en primer lugar, el hándicap de la logística de traslado y el desmontaje in house.
En el pasado, durante el transcurso de una feria, solicitaron a 3DZ unas muestras de Onyx con refuerzo de kevlar. Al encontrarse con el problema del lote defectuoso de lámparas, vieron que las características de la muestra encajaban con sus necesidades. Encargaron una prueba para testar la solución de Markforged propuesta por 3DZ y después del análisis y cálculo de costes, se decidieron por la impresora 3D Mark Two de Markforged. La cercanía con un proveedor que conoce a la perfección su producto, el servicio técnico tan cerca de la empresa, recibir el material en cuestión de horas, fueron factores también decisivos a la hora de decantarse por 3DZ. Al tener a su disposición todas las tecnologías 3D y equipos de 1ª calidad, 3DZ pudo ofrecer la solución que realmente se adaptaba a sus necesidades.
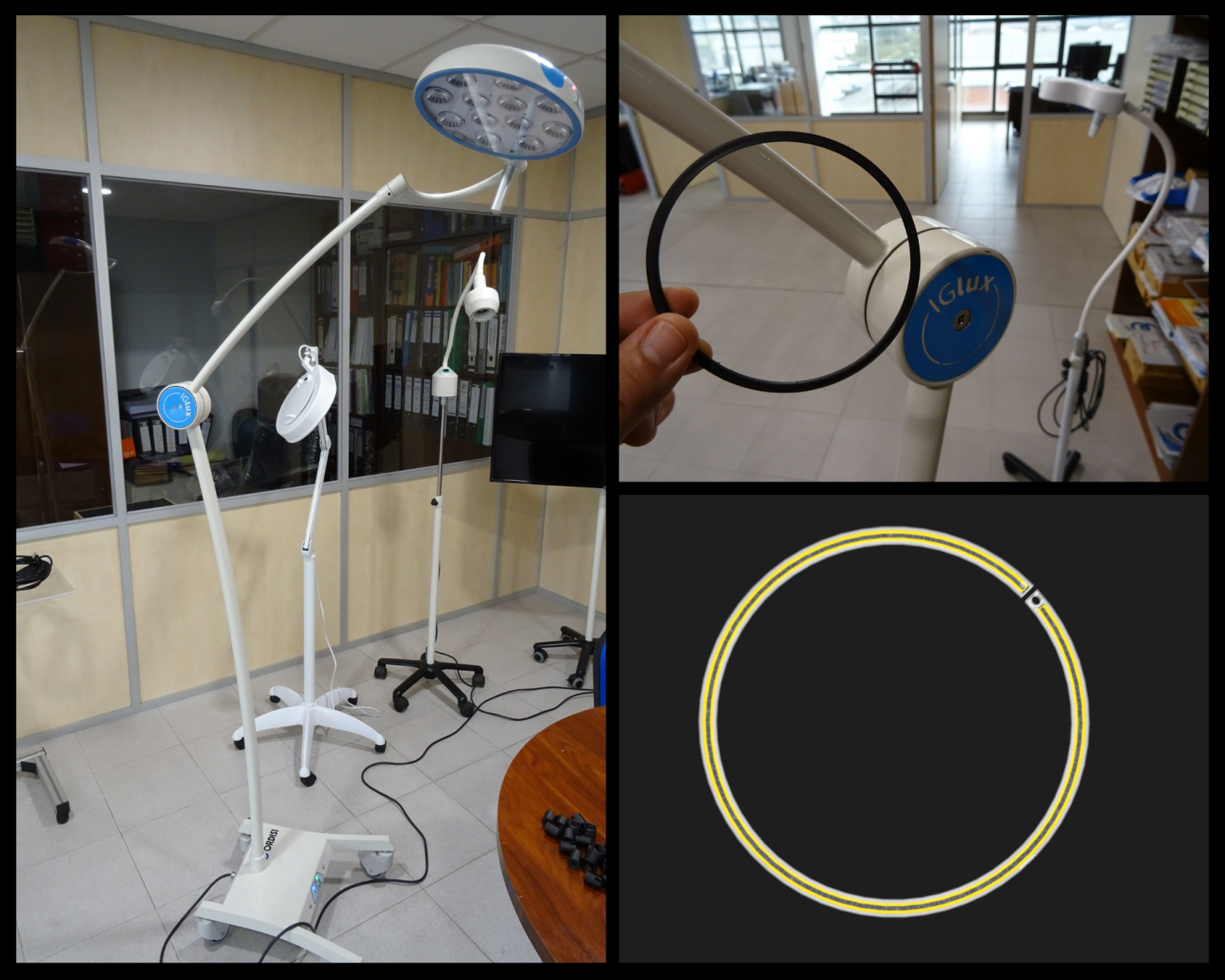
Más de 6.700 horas al año de impresión
Uno de los motivos por los que se decantaron por una Mark Two fue el acabado, “aunque la mayoría de las piezas que fabricamos con la máquina no estén a la vista, algunas si lo están y nos interesa transmitir un acabado fino que no deje ver los hilos de impresión como ocurre con otras impresoras” señala Alberto López, Responsable de Calidad en Ordisi.
Ordisi fabricó una pieza de recambio abierta compuesta por Onyx, con refuerzos de fibra continua de Kevlar a lo largo de todo el contorno, que podía ser montada por el propio cliente final de forma autónoma y sin desmontar absolutamente nada.
La producción se realizó en cuestión de días, en mucho menos tiempo que si el equipo hubiera seleccionado un método de fabricación tradicional. Descubrieron además que les permitía fabricar gran cantidad de componentes en función de su demanda llegando a explotar la máquina 24/7 para alcanzar más de 6.700 horas de impresión al año. Dos años y medio después, tras más de 15.000 horas de impresión han comenzado a expandir sus capacidades de impresión con un equipo X3 de la gama industrial de impresión 3D de Markforged.
“A veces hacemos la broma: quien más trabaja en la empresa es la Mark Two”
En la actualidad ambos equipos están imprimiendo una o varías bandejas de impresión durante la jornada y una bandeja por la noche, justo antes de terminar el día, optimizando al máximo su rendimiento. “Estamos haciendo producciones de 24horas para tener una o varias bandejas impresas todos los días. Cuando nos vamos por la noche dejamos la máquina imprimiendo hasta las 8am del día siguiente que volvemos a abrir. Las piezas grandes las imprimimos durante el día para que la máquina nunca pare y las pequeñas por la noche para aprovechar 15 horas seguidas de impresión”, señala Alberto López, “poco a poco estamos sustituyendo todas las piezas de mecanizado por piezas hechas con la tecnología Markforged y actualmente estamos estudiando qué utillajes hacer y cómo hacerlos para conseguir producir más rápido.”
Otro de los usos que Ordisi ha dado a sus máquinas es el de prototipado. La Mark Two les ha permitido prototipar para avanzar más rápido en el desarrollo de nuevos productos detectar posibles fallos e ir mucho más directos a la fabricación del molde de inyección y sin errores.
Ordisi diseña para la fabricación aditiva. Con la adquisición y uso de las máquinas se dieron cuenta que no podían calcular un precio optimizado de un diseño pensado para ser fabricado con otra tecnología. Vieron fundamental adaptarse a la máquina para trabajar, los números cambiaron radicalmente trabajando a favor de la tecnología vs. los cálculos iniciales. “Calcular la amortización o el ahorro de costes que ha supuesto la adquisición de las máquinas es difícil de saber. El precio de la máquina es relativo al uso que le das, es una herramienta y va a depender de las horas. No importa tanto el coste de la máquina sino cuánto es el coste final de la pieza. Y no solo el coste sino los beneficios que conlleva” describe Alberto López.
Otra de las ventajas que destaca Ordisi es el escaso mantenimiento de la máquina. “La tasa de error es prácticamente cero. Para que os hagáis una idea, si Ten una sola bandeja de impresión de piezas pequeñas salen unas 50 unidades, en 3 años de uso hemos podido desechar como mucho 20-30 piezas”, señala López, “la máquina es muy fácil de utilizar, nos llevó escasos dos meses optimizar los diseños”.
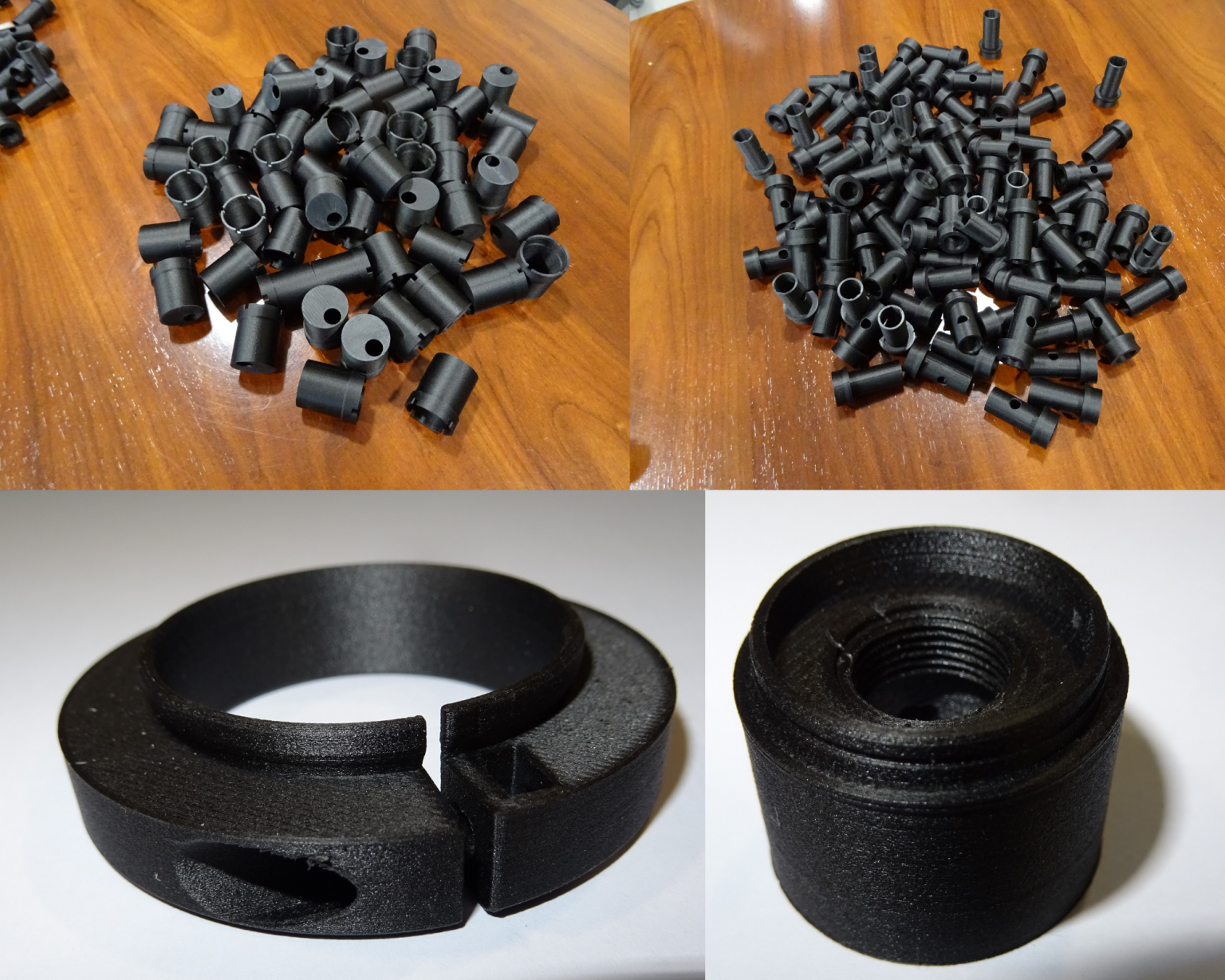
Las ventajas de la impresión 3D para Ordisi
- Rápida iteración, para poder probar diferentes versiones y así dar con una forma eficaz de sustituir la junta defectuosa de una forma rápida. Horas en lugar de semanas y a un coste menor.
- La flexibilidad de diseño permitió fabricar este recambio de fácil instalación.
- Fabricación directa, sin necesidad de utillajes.
- Sin necesidad de externalizar, con el coste y tiempo añadido que ello conlleva. Esto además, impide poder realizar un mayor número de pruebas.
- Los costes para el envío de un paquete para un recambio de pocos gramos son muy inferiores a los costes de ida y vuelta del paquete voluminoso necesario para el envío de las lámparas completas.
- La calidad y acabados de las piezas piezas en Onyx y poliamida con fibra de carbono permiten usarlas en múltiples aplicaciones, empezando a fabricar con esta misma impresora 3D una gran cantidad de componentes para sus lámparas.
- Planificación de la producción por tandas.
- Un trabajo continuo y desatendido. Es un equipo robusto, preciso y fiable, que permite producir piezas de gran calidad.
- El único post proceso es la eliminación de soportes en caso necesario y pueden ser retirados a mano.
- En la actualidad, en gran parte de su producción, se emplean piezas impresas que anteriormente se realizaban por mecanizado. Llegando a imprimir más de 1500 horas en 2 años y medio.
- Cada vez son más las aplicación que encuentran para las piezas de Markforged. A día de hoy, en gran parte de su producción se emplean piezas impresas en 3D.
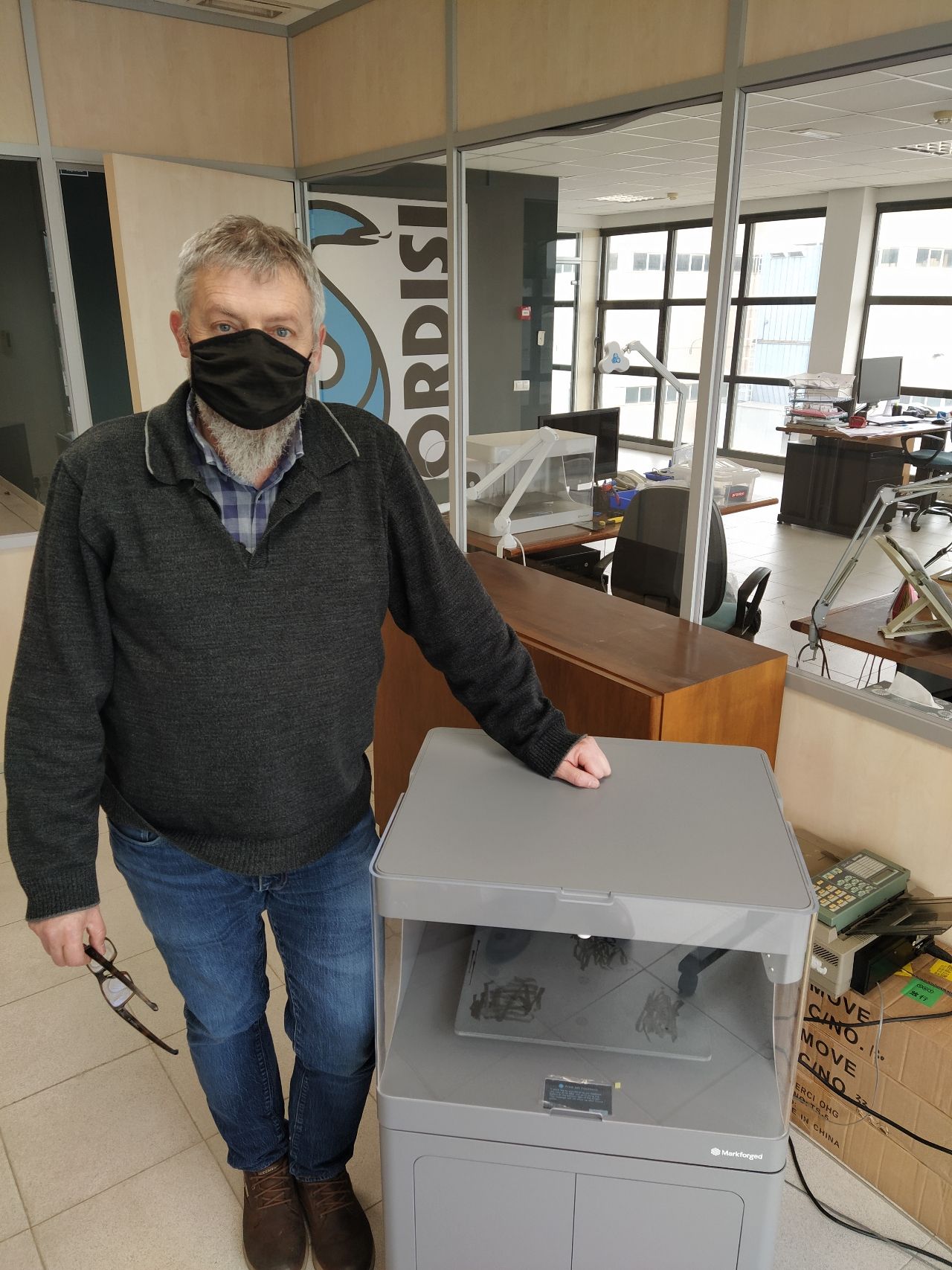
¿Quieres ahorrar tiempo y costes con la tecnología 3D?
Descubre cómo con 3DZ, el distribuidor nº1 de Europa de las mejores marcas de impresoras y escáneres 3D. Por ello, nuestra gama de productos también incluye Markforged, máquinas que combinan la flexibilidad de la impresión 3D con la notable resistencia de los materiales que pueden utilizarse como refuerzo de los materiales base de Nylon u Onyx, como la fibra de carbono, la fibra de vidrio, el Kevlar® y la fibra de vidrio de alta temperatura.
¿Quiere evaluar con uno de nuestros expertos cómo optimizar tu proceso de producción, aprovechando el potencial que ofrece la impresión 3D para este tipo de aplicaciones? 3DZ te ofrece un servicio de consultoría gratuito para entender tus necesidades específicas y te apoya en la introducción de tecnologías de fabricación aditiva.